How we deliver safe, quality construction on time
- Each and every employee in the field is put through a rigorous, 6-7-hour orientation before they are allowed to report to the field for work. This includes the OSHA certified Heavy Equipment Safety Course, Fall Protection Course, Confined Space Entry Course, Company Safety Manual Overview, and all Company Policies. This ensures that all new employees have all the information they need to avoid or eliminate the risk of injury.
- All applicants are required to possess an OSHA 10-hour card for construction; and an OSHA 30-hour construction card for supervisors before reporting to the field. This is an industry standard.
- Our Company requires participation in the Short-Service Employee Program. Every new employee is a short-service employee, meaning they have less than 6 months with the Company. They can be readily spotted on the jobsite by the green hard hat they wear. Each short-service employee is assigned a mentor when they report to the field. The mentor teaches the SSE (short-service employee) the safe, correct, Smith way that things are done and answer any questions the SSE may have. If, after 180 days the SSE has learned the Information set forth in the SSE Checklist, he is given an orange hard hat in place of his green one.
- All employees are issued 2-way radios with their initial PPE issue to ensure there is no lapse in communication between laborer and operator. This ensures instant communications when laying pipe, etc., avoiding possible injury and saving time by not requiring the operator to leave the cab or the laborer to move around in the operator’s area of operation.
- On-Site Safety Supervision: The objective is for the Safety Coordinator to visit each jobsite numerous times per week to ensure all safe practices and company policies are being followed. There is a close relationship between the Safety Coordinator and the field employees as they know he is looking out for their best interests. One of his responsibilities is to identify any green hard hats and to visit with those people to ensure that they are clearly aware of their role in the process and that there are no questions. Statistically a person is hurt or killed in the first 6 months on the job and our safety program ensures the utmost care is taken to avoid that risk.
- Reporting Near Misses: All employees are encouraged to report all Near Misses, however inconsequential they may seem. Near Misses are immediately investigated just like a full- fledged incident or accident because if it happened to one person, it is likely happening to others. The only difference between a Near Miss and accident is there was no one in the “line of fire” at the time. Investigation findings and corrective actions are then communicated to all field employees so that everyone can benefit from this opportunity, hopefully avoiding any injury that could arise in the future from these events. It is important to note that no one is in trouble for reporting or being involved in a Near Miss. These are looked at as learning opportunities.
These are just a few of the ways our Company strives to “stay ahead of the curve” when it comes to leading the way in safety for other area site contractors to follow. Our previous experience with the energy companies in Pa has positioned us to be leaders in pro-active safety (anticipating and planning for undesired events) instead of being re-active (always reacting and allowing undesired events to direct your energies toward “always playing catch up.” It is non-productive to have production as one entity and safety as the other. We have created a safety culture where “safe production” exists as one entity. Nothing we do is worth getting hurt.
Reach Out To Our
Expert Team!

Address: 715 W. Main St, Tavares, FL 32778

Phone: 352-253-2219

Fax: 352-609-5927

Email: southoffice@smithsitedev.com
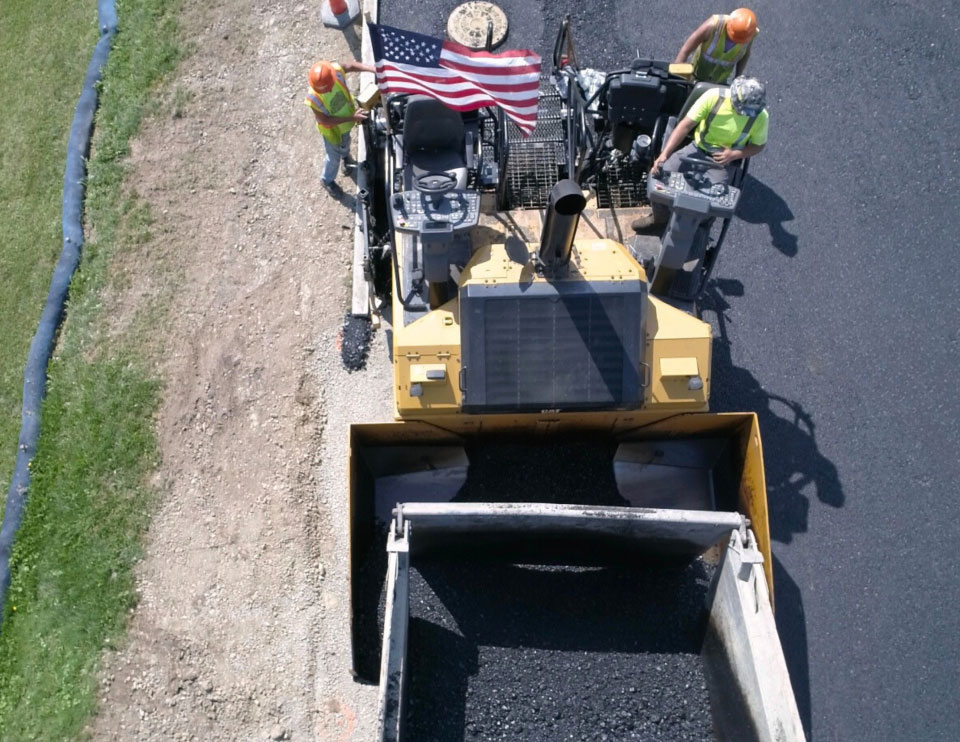